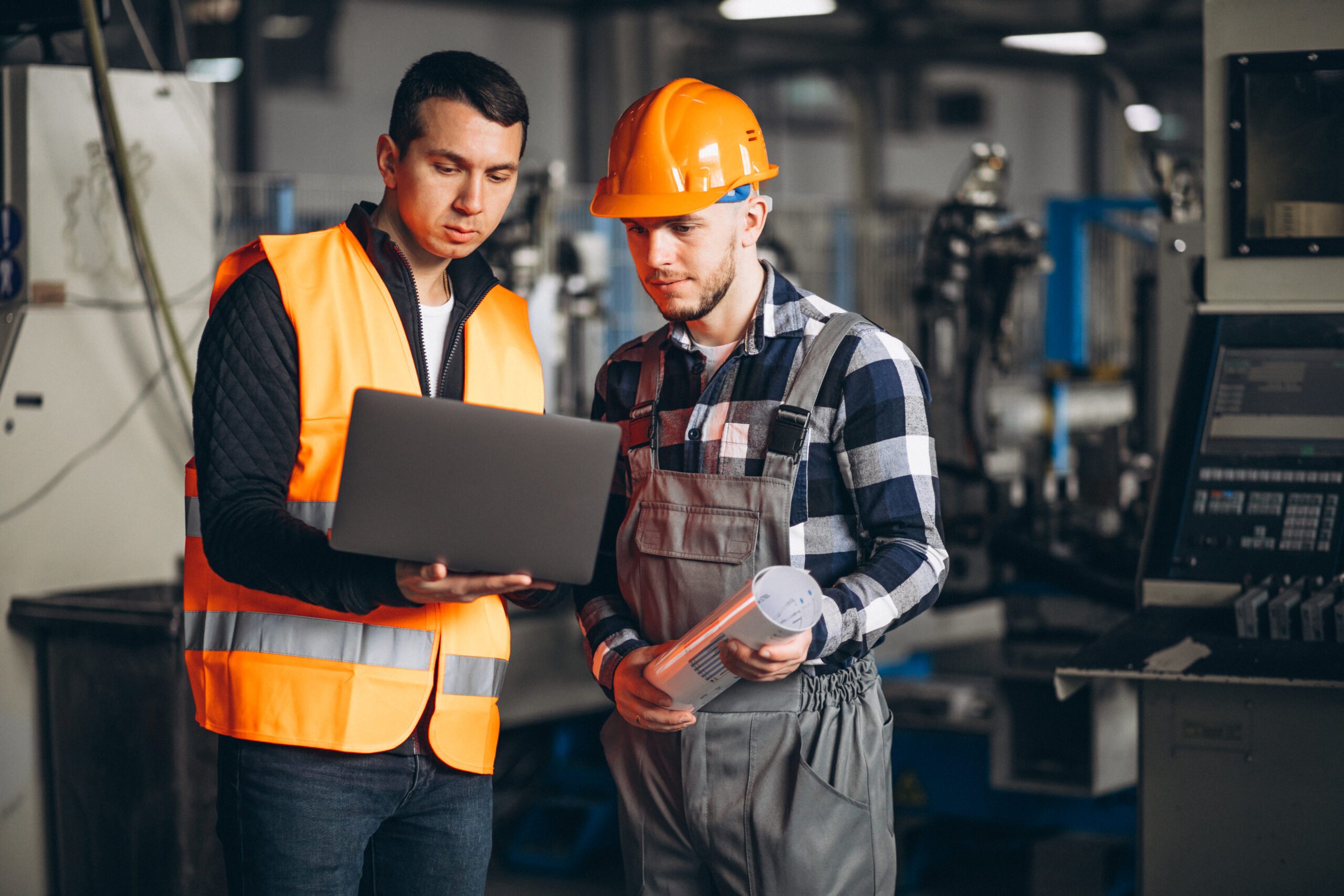
You’ve decided to embrace the tech revolution, upgrade your manufacturing operations, and boost productivity with a shiny new IT system. Exciting, right?
But, and it’s a big but, diving into this without a solid plan could prove problematic.
We get it – change is hard, especially when it comes to integrating new IT systems into your well-oiled production machine. We’re not here to preach about the wonders of technology; instead, we’re here to have an honest chat about the potential pitfalls when jumping headfirst into a new IT implementation without a solid game plan.
Let’s talk about the latter and why skipping the planning phase could turn your IT adventure into a headache.
1. Budget Blues:
Picture this – halfway through the implementation, the costs start piling up faster than you can say “ROI.” Without a meticulous plan, you might find yourself bleeding money on unforeseen expenses, ranging from unexpected software customisation needs to prolonged downtime that disrupts your production schedule.
There’s steps you can take to negate this especially by taking the time to conduct a thorough cost-benefit analysis before embarking on your IT system implementation journey. Factor in not only the obvious upfront expenses but also potential hidden costs. By understanding the financial landscape comprehensively, you’ll be better equipped to make informed decisions, ensuring that your investment aligns with your business goals and doesn’t spiral out of control.
2. Downtime Dilemmas:
In the fast-paced world of manufacturing, every minute counts. Poorly planned IT projects can lead to downtime nightmares, transforming your bustling production floor into an eerily quiet space where machines sit idle and employees twiddle their thumbs. The impact isn’t just internal; your customers, accustomed to the precision and efficiency of your operations, are left wondering where their orders are in the void of unexpected delays.
Let’s face it – time is money, and wasted time is just… well, waste. It’s crucial to recognise that minimising downtime isn’t just a goal; it’s a necessity for maintaining your competitive edge. To avoid these production pitfalls, invest the time upfront to plan your IT implementation, accounting for potential disruptions and creating strategies to minimise downtime.
The result? A seamlessly integrated system that keeps your production humming and your customers satisfied.
3. Compatibility Catastrophes:
You’ve got your eye on a sleek new system, all the fancy new features on show after a big sales pitch on how it could transform your manufacturing operation – Surely it’s a no brainer?
Stop right there. The biggest thing many companies overlook when implementing and integrating a new piece of technology into their manufacturing floor is not understanding if it’s compatible with your existing tech infrastructure. Neglecting this crucial detail can result in a tangled mess of software conflicts, leaving you with more headaches than solutions.
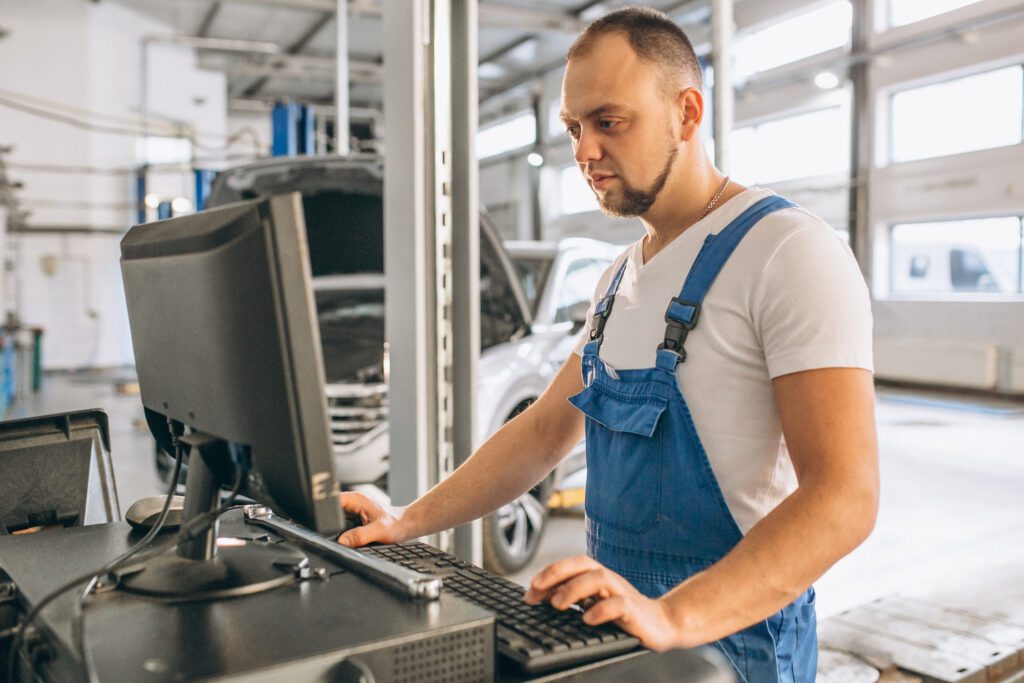
Now we’re not going to do the hard sell here but we’d suggest this is where an IT partner can be invaluable. Understandably, knowing the in’s and outs of an IT system isn’t your day job, you’ve not got years of experience so this is where investing in a partner who does can help ensure that your new IT system slots in seamlessly to your existing infrastructure.
4. Security Slip-Ups:
In the age of relentless cyber threats, leaving the factory gates wide open for attacks is simply a no-go. Ignoring IT security in your manufacturing IT plan is a recipe for disaster. Your sensitive data becomes a prime target, and the safeguarding of your proprietary manufacturing techniques hangs in the balance.
To combat this, look at implementing robust encryption measures to shield critical production data, fortify access controls to ensure only authorised personnel have entry, and stay ahead of evolving cyber threats through regular updates and specialised employee training. By adopting a proactive security stance, you not only protect your valuable assets but also fortify the backbone of your manufacturing operations against potential disruptions.
Remember, prevention is your first and best line of defence on the manufacturing floor.
5. Employee Engagement
Employee engagement and training are pivotal components when planning the implementation of a new IT system in manufacturing. Your workforce is at the heart of your operations, and their seamless integration with the new technology is key to a successful transition.
Engaging employees from the early stages creates a sense of ownership and collaboration, making them stakeholders in the process rather than passive participants. It’s crucial to conduct comprehensive training sessions tailored to the specific needs of your manufacturing environment. Ensure that employees understand not just how to use the new system but also how it aligns with and enhances their daily tasks.
Add in regular feedback loops and open communication channels are essential to address concerns and adapt the training approach as needed. A well-trained and engaged workforce not only minimises the risk of resistance to change but also maximises the efficiency gains that the new IT system promises.
Conclusion:
To wrap up, embarking on the journey of implementing a new IT system in manufacturing can seem like a big task. Whilst it shouldn’t be underestimated, ultimately with some thoughtful planning that involves an investment of time, energy and resources then it doesn’t need to be difficult.
As the old saying goes, fail to prepare, prepare to fail.
Ready to embark on your IT journey? We’re here to help. Contact us today!